Aluminium
Aluminium is a common material used every day in consumer goods like cans and foil. The main properties of this metal are its low density (2.7 g/cm³), its resistance to corrosion, and its high thermal and electrical conductivity. Its ductility and low weight make it an ideal replacement for steel in certain areas where its low density compensates for its decreased resistance. For these reasons, it is widely used in the aerospace, aeronautics, vehicle, and defence industries.
It is also one of the key materials used in the MotoGP bikes of Marc Márquez and Pol Espargaró, especially the chassis, although it may also be reinforced with carbon fibre when used in this way. The characteristics of this lightweight, flexible metal make it ideal for this basic part of the structure, as MotoGP chassis must strike a balance between rigidity and flexibility.
The front forks also use aluminium, with the use of certain alloys being mandatory. The brake levers, radiators, footrests and some of the engine housing are all made of aluminium. The rules also permit the use of aluminium in the rims, although this tends to be more common in the lower classes.
The alloy most used in competition is 7075, one of the best, in which aluminium is combined with zinc and small quantities of magnesium and copper. Also, various special treatments may be used to improve its properties.
Aluminium has a silver colour and the symbol Al on the periodic table. It is the third most common element on planet Earth, although it is not normally found in its pure form. Usually, it has to be refined and extracted from rocks such as bauxite. Parts from this material are generally forged, putting the metal into high pressure presses. It can also be smelted, when it is poured into moulds that have the desired shape, or machined, when the part is created by cutting off fine chips.
Magnesium and titanium, lightweight materials used in MotoGP
Carbon fibre
CFRP (Carbon Fibre Reinforced Polymer) is a high performance, extremely lightweight composite material. It is formed of a resin and a fabric made of carbon threads that are just a few microns in diameter (from 0.004 to 0.01 microns).
It is extremely rigid and has great mechanical resistance, as well as being very light. It can also withstand high temperatures, humidity, and solvents well.
CFRP is used extensively in MotoGP, and more and more parts are being made of this material. Fairings and mudguards are made of carbon fibre, as are some protections and auxiliary parts. In recent seasons we have seen how it has started to be used to manufacture swingarms and shock towers, either replacing them or to strengthen aluminium ones.
Currently, the rules forbid the use of carbon fibre in rims, although they can be found in the auxiliary industry.
Although preparation and a long and expensive manufacturing process are needed to create pieces using this material, it has earned a place in many areas of present-day industry.
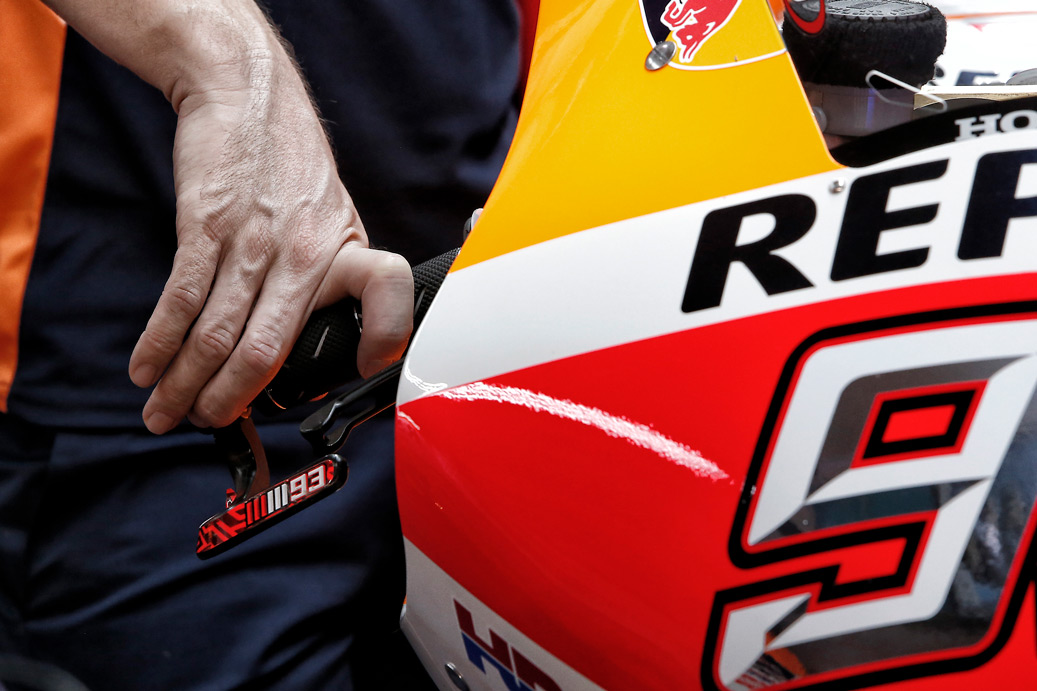
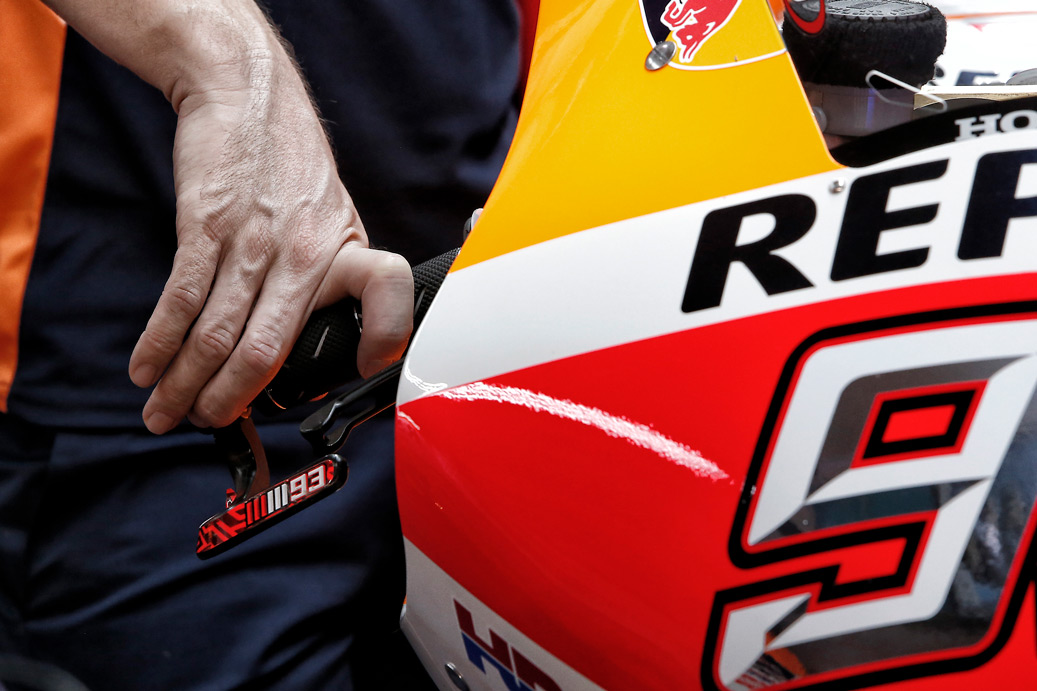
One of the most usual manufacturing methods is moulding, in which a resin mixed with a catalyst that reduces the curing process is applied to a mould. After this, sheets of fibre are placed in the mould and arranged. It must be firm and compact, with no air between the fibres. To do this, the parts are placed in bags to which a vacuum is applied to extract the air and compact everything.
More resin is then introduced with the help of this constant vacuum. In addition, to accelerate the process, the bags with the parts are cooked in an autoclave, from which they emerge with the desired characteristics after several hours.
The process used to obtain carbon brakes for the top class is totally different. These are carbon/carbon discs, with a composition that lacks the ceramic elements normally found in street vehicles. Although it reduces their lifespan drastically to just a few thousand kilometres, this option gives them greater braking capacity.
They can take up to 9 months to manufacture, and part of this time is spent in a 1000°C kiln in a controlled atmosphere. This process, which is known as “chemical vapour deposition”, causes the particles of carbon contained in a gas, normally methane, to be deposited on the final product.
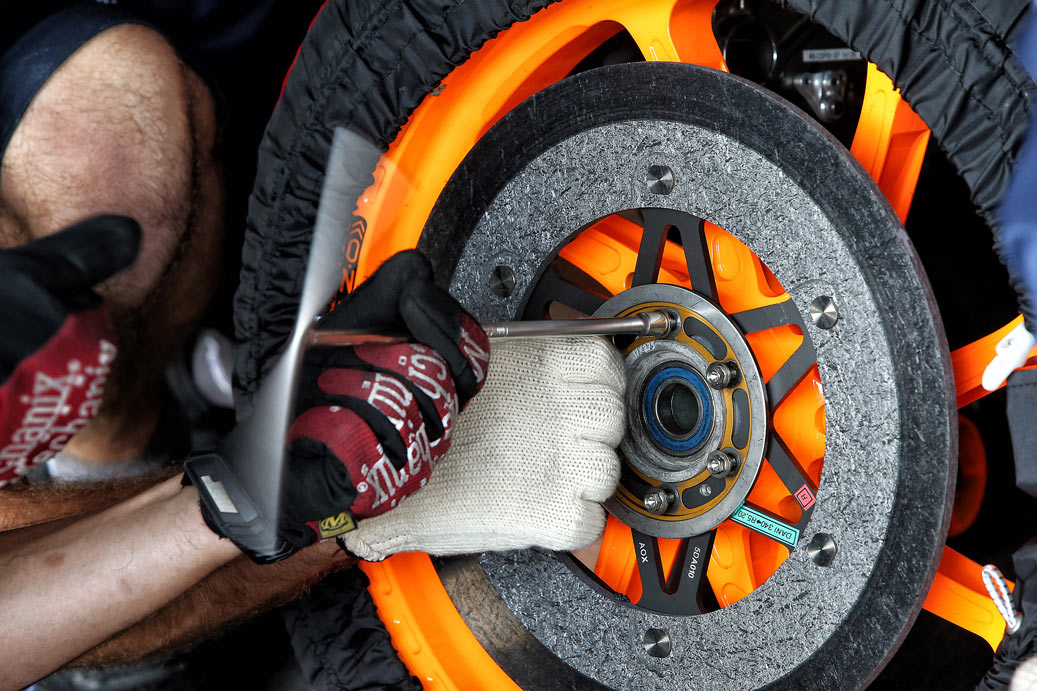
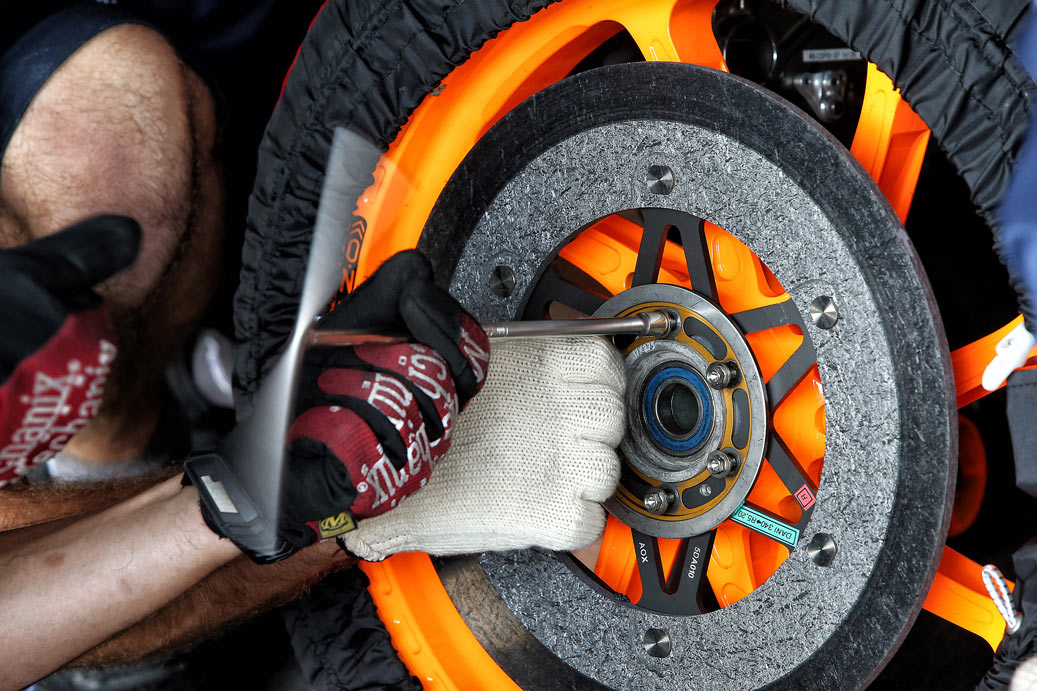
The flexibility of aluminium and the lightness of carbon fibre are qualities that makes these materials ideal for both the top class and the most advanced aeronautics. It’s no wonder that the best riders and their cutting-edge machines also need these highly advanced components.